Engineering Business
Noritake's Growth Strategy
Main products
Heating Furnaces, drying furnaces, agitation equipment, filtration equipment,Carbide-tipped circular sawing machines, circular sawing cutting machines, etc.
-
Static mixer -
Roller hearth kiln -
Coolant filtration system -
Rotary kiln -
Carbide-tipped circular sawing machine (Thin Cut Master) -
Circular sawing cutting machines
Performance in Fiscal 2023
Sales of our mainstay heating and drying furnaces increased, driven by steady demand for LiB (lithium-ion batteries). Sales of agitation equipment were strong, particularly in our major field of chemicals. Filtration equipment saw a slight decline in sales, as the recovery in demand from the automotive and machine tool sectors was offset by weak sales in the bearings sector. Sales of carbide round saw cutting machines for automotive parts declined, while sales of concrete cutter fell below the previous year due to decline in public works projects. As a result, net sales in the engineering business were 28.558 billion yen (an increase of 10.2% from the previous year) while operating profit was 2.194 billion yen (an increase of 7.0% from the previous year).
Progress of the 12th Three-year Business Plan
Fiscal 2023 was a year of significant growth with record sales of agitation equipment in the fluid business, and we are now within reach of the ambitious target of 30 billion yen in sales for the engineering business. In fiscal 2024, the final year of the 12th Three-year Business Plan, we are committed to achieving our budget target and securing profits to move to the next stage. Under these circumstances, we will strive on recovery for products that remained sluggish due to market conditions. Heating and drying furnaces for LiB show continuous growth, and we expect that customers will continue to invest actively in the future as EV (electric vehicles) become more advanced. To expand production capacity for these products, we are constructing a new building at the Komaki Plant, continuing reorganization, and strengthening collaboration with overseas vendors.
Furthermore, we will continue to develop next-generation products in the electronics field, while also exploring new areas such as functional materials, new batteries, and catalysts.
Growth Strategy
In the heating business, which handles heating and drying furnaces, orders for LiB post-process drying equipment have been growing in the environment field. We will continue expanding these sales in Japan and overseas in fiscal 2024. In addition to our mainstay LiB pre-process heating furnaces, we intend to develop it into a second pillar for our business. In the fluids business, which mainly handles agitation and filtration equipment, we have made progress in the environmental and electronics fields. In the environmental field, we began deliveries in fiscal 2023 of the Smart Briquetter, a system that solidifies and compresses sludge produced in filtration processes, separates and recycles the grinding oil, allowing reuse of both sludge and oil. In addition, from the perspective of reducing food waste, we are also promoting the commercialization of heat sterilization equipment that can utilize out-of-specification produce such as fruits and vegetables. In the electronics field, we are collaborating with a semiconductor equipment manufacturer to develop an exhaust gas removal system for the semiconductor manufacturing process. In the area of wellbeing, we are focusing on the development of a column less continuous purification system for pharmaceuticals. This is the industry's first initiative to sequentialize process of refining processes of biopharmaceuticals, and we are participating in exhibitions and other events.
While the heating business accounts for 70% of total sales in our business portfolio, we are now increasing the number of new products in the fluid business and accelerating development to optimize the balance between our businesses.
MESSAGE
Fostering a culture of challenges and enhancing opportunities for self-improvement to drive the growth of our business
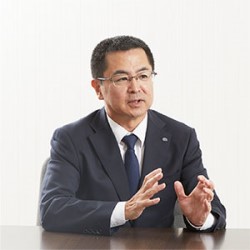
Group General Manager of Engineering Group
Yoshiaki Takaba
In March 2024, we installed a hydrogen-fired heating furnace at our test center and began pilot operation. This allows us to observe the effects on products when switching from electricity or gas to hydrogen fuel for firing. Although we have only received a few requests for testing so far, we expect this to attract interest in the future.
“Challenge” is indispensable in the grows fields we are targeting, such as carbon neutrality, advanced medical care, and semiconductor manufacturing. It is therefore essential to foster a culture where employees from all generations—new hires, mid-level employees, and veterans alike—can take on new challenges. We aim to create an atmosphere where everyone feels free to express their opinions, regardless of hierarchical relationships, with a focus on employees actively pursuing their skill development and career paths through acquisition of qualifications and expertise. Fiscal 2023 was a busy year throughout. While it is positive for our performance, it made it difficult for employees to dedicate time to their studies, which may be a risk to future growth. We will implement strong labor management to ensure that all employees have time for self-improvement, which will lead to further growth of our company.