Grinding Basics
Grinding Support
Safety
Miscellaneous Information
Information on fixed abrasives
- Catalog Download
- List of Catalog Download
- Grinding & Polishing Technical Information "NORITAKE TECHNICAL JOURNAL"
- About Our Sales Offices
What are the usage conditions for your wheels?
The usage conditions for wheels can be divided into four categories according to morphology: normal, shedding, loading and glazing. Observing the usage conditions of your wheels in order to choose more appropriate wheels is the first step to improving grinding processes.
(1) Normal type
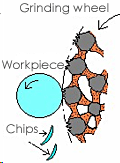
When the cutting edges of abrasive grains become dull by increasing the cutting infeed, grinding force increases. At this time, cutting edges are cleaved so as to expose new cutting edges adequately. Thus, the normal type means that ideal grinding action is usually continued, recovering original sharpness again. In such the normal type as this, the cutting edge intervals (from original sharpness to next sharpness) of abrasive grains are adequately kept, grinding wheel wear is remarkably less in comparison with the shedding type since chips are not welded. Consequently, the workpiece surface is finely finished and grinding precision is high. Though the grinding force of this type is higher than the shedding type, it is lower than other loading type and glazing type.
The grinding wheel and working condition are to be selected so that such the grinding as this is usually performed as grinding work.
(2) Shedding type
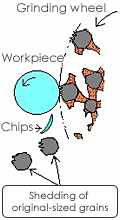
This phenomenon is caused when the grade of grinding wheel is extremely softened for the grinding condition. The grinding wheel cannot be withstood to the grinding force and original grains fall by the destroying of bond.
Under such the condition as this, since the cutting edge intervals of abrasive grains are wide and the workpiece is usually ground by sharp cutting edges, though sharpness is extreme, the grinding wheel surface becomes rough, form is in disorder, the precision and finished surface roughness of workpiece become remarkably worse and the grinding wheel is also considerably worn.
(3) Loading type
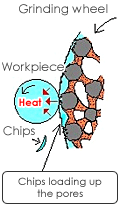
This phenomenon is caused when the softened and viscous materials such as aluminum, stainless, etc., are ground. Also, the phenomenon is easy to cause when chips are adhered to cutting edges (built-up edge) and casting iron, stone material, etc., are ground by dry process. Thus, chips are caught into pores to clog chip pockets. In these two types, the grinding force becomes large. Especially, in the case of former, vibration is easy to occur and “Peeling” or “Chatter” most especially occurs on the finished surface.
(4) Glazing type
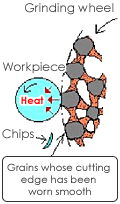
When grade is excessively hard, abrasive grain is hard, toughness is low and the wheel speed is over for grinding conditions, the cutting edges of abrasive grains become dull by proceeding the grinding and the sharpness becomes very worse, grinding force is large, heat generation mostly occurs and chatter and burn mark also occur much.
The condition of your chips is also important information.
When grinding, the workpiece is ground by the cutting edges of abrasive grains, discharging fine chips. The shedding, glazing, etc. of grinding wheel occur from the relationship between this chip shape and each cutting edge of abrasive grain. This phenomenon occurs from a constant timing. Consequently, the grinding mechanism controls condition for that time.
Chips ground by grinding are fine similarly with chips ground by turning tool and milling cutter. The chip is divided into five types as follows:
(1) Flow chip

Ribbon shape chip occurs when grinding wheel sharpness is good.
(2) Shear chip
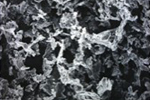
This chip occur when grinding wheel sharpness is good.
When brittle materials are ground, chips are discharged.
(3) Peeling chip
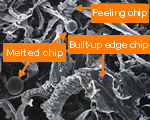
Powder chip occurs when grinding wheel sharpness becomes dull.
(4) Built-up edge chip
Chips are adhered and accumulated on grinding wheel face and these chips are made of texture so as to be the same as built-up edge.
(5) Melted chips
These chips are spherical or semi-spherical by melting when powder chips are scattered by over-heat. This is mostly found when ground by loaded or glazed grinding wheel.
Depth of cut for abrasive grain
When selecting the grinding wheel and various working conditions suited for grinding work, first, the condition when the grinding wheel contacts with the workpiece and the workpiece is finely ground by the grain cutting edges must be understood. It is necessary to understand the infeed that each grain cutting edge grinds, that is, about the grain depth of cut.
The grain depth of cut varies by the following items:
1) Grinding wheel speed and workpiece speed
2) Grinding wheel sizes and workpiece sizes
3) Infeed amount
The above relations are explained by the following figure.
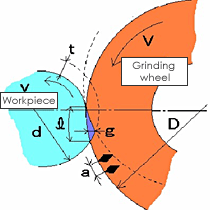
D: Diameter of grinding wheel (mm)
d: Diameter of workpiece (mm)
V: Wheel speed (m/min)
v: Workpiece, wheel speed (m/min)
f: Feedrate
t: Grinding wheel infeed amount (mm)
g: Grain depth of cut (mm)
ℓ: Length of contact arc (mm)
a: Grain cutting edge interval (mm)
(1) Grain depth of cut (g)
When the grain depth of cut (g) is geometrically found, the following formulas are established every grinding type.
Cylindrical grinding | ![]() |
---|---|
Internal grinding | ![]() |
Surface grinding | ![]() |
As the grain depth of cut (g) increases, the load exerted on the grain increases, and grains are removed. On the other hand, if (g) is smaller, the load exerted on the grain decreases and the grain experiences abrasion wear. These formulas clarify the relationship between grinding conditions and grinding wheel actual hardness on grinding.
Condition |
Wheel speed (V)* | Slow![]() |
---|---|---|
Wheel speed of workpiece (v)* | Quick![]() |
|
* If v/V is constant, the actual hardness on grinding will not change even if v and V change. | ||
Grain cutting edge interval (a) | Wide![]() |
|
Diameter of grinding wheel (D) | Small![]() |
|
Diameter of workpiece (d)** | Small![]() |
|
Infeed amount of grinding wheel (t) | Large![]() |
|
Grain depth of cut (g) | Large![]() |
|
Grinding wheel actual hardness on grinding | Softly acted.![]() |
** For internal grinding, large and small are reversed.
(2) Length of contact arc (I)
Length of contact arc (I) is represented by the following formula.
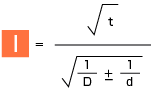
As the length of contact arc (I) increases, grain depth of cut (g) decreases, which has a hardening effect on the wheel. Conversely, a decrease in the length of contact arc (I) can be understood to have a softening effect.
The length of contact arc is controlled by the grinding method as well as by the wheel diameter, the workpiece diameter and the wheel infeed amount, and it increases in the order shown below.
cylindrical grinding < horizontal surface grinding < internal grinding < vertical surface grinding, double-sided surface grinding
Accordingly, the wheel chosen for use with a horizontal surface grinder should be softer than that used with a cylindrical grinder. For a vertical surface grinder, an even softer one should be chosen and the length of contact arc should also be reduced.