Promote activities for improving quality
Sustainability Initiatives
- Sustainability at Noritake
- Contribute to the Global Environment
- Contribute to a Convenient Society
- Contribute to the People’s Well-being
- Strengthen the Foundation
- Management Structure
Quality Policy
The Noritake Group has established a Quality Policy for providing quality products and services that satisfy our customers.
Noritake Group Quality Policy
Based on the corporate motto of "Good Quality, Export and Co-prosperity", the Noritake Group will continue to respond to the trust and the expectations of customers around the world by providing quality products and services that satisfy our customers.
- (1)We provide safe and secure products and services from customers’ viewpoints.
- (2)Each and every person in all our organizations continues to work on quality improvements.
- (3)We comply with laws, regulations and requirements related to products and services.
- (4)We appropriately disclose necessary information for our customers.
Quality improvement promotion system
From FY2023, the "Quality Committee" was established under the Sustainability Management Committee in order to maintain and continue to improve the structure by which we promptly and reliably provide the "quality products and quality services" that customers demand. The Quality Committee develops the quality policy, quality targets and action plans, with the aim of improving quality throughout the entire Group.
Key activities in FY2023 include internal quality audits on the heads of business units to check the internal dissemination of the quality policy and the progress of activities aimed at achieving materiality goals, thereby strengthening management capabilities in the process.
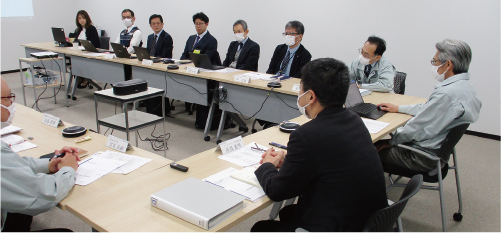
Activities to enhance manufacturing
Noritake is a manufacturer that was born from the passionate desires of the founders to "make porcelain with exquisite craftmanship and impeccable whiteness." Based on this spirit, the Noritake Manufacturing Committee was established in 2011 to improve the quality of our products and services.
In 2011, we started basic development activities under the "Manufacturing 3-1 (M3-1) Activities" for manufacturing departments. To ensure stable production, we have implemented a system that is the foundation for safety (2S and standardization). In addition, we have integrated "quality activities" for the engineering division and we are evolving them into activities that promote manufacturing and technology together. Since 2016, as basic enhancement activities, we have expanded our activities to develop management standards and systems that control the five major missions of our production sites: Safety, Quality, Production, Cost, and Human Resources.
We have expanded our manufacturing activities for sales, engineering, development, management, planning, and administration as "S3-1 activities," and are currently promoting activities based on the two pillars of "M3-1 activities" and "S3-1 activities."
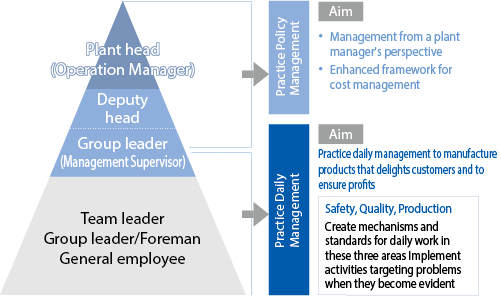
M3-1 activity (manufacturing and engineering divisions)
Throughout our M3-1 activities, we stress the concept of "Customer First, Safety First and Quality First" in our manufacturing and engineering departments, and promote basic enhancement activities based on the recognition that achieving these three "Firsts" is important for continuing to contribute to society through our business.
Basic enhancement activities
In our basic enhancement activities, we are focusing on the control of Quality, Cost, and Delivery. Among the five major missions of the production site, we have identified Safety, Quality, Production, and Cost as priority areas for action. We are implementing initiatives to enhance these areas, aiming to improve the quality of daily management. Plant managers have been leading basic enhancement activities based on the principle of local physical goods. These have now been integrated into the management system as a continuous framework, and operations have commenced.
The Noritake Group's 12 plants hold activity meetings for local physical goods, where the activities for the five major missions are recognized in the form of mutual study of the plant sites. Furthermore, starting in FY2024, each business unit will independently promote management capability enhancement and on-site operational capability enhancement. We will also hold activity report meetings where participants will engage in discussions and share best practices for wider implementation across the Group.
Plant roles by qualification
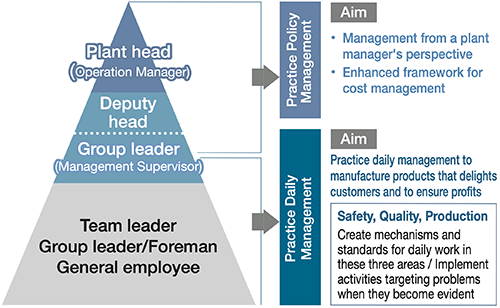
Quality activities
As part of our efforts to improve quality, we are promoting "Obeya" activities and production preparation activities, and have continued the Quality Activity Study Group FY2021.
Obeya
In Obeya, or common room, activities, site administrators such as plant general managers gather with relevant personnel from manufacturing, production technology, quality assurance, product development, etc., to hold cross-departmental meetings to promptly carry out activities for making corrections and improvements through factor analysis and discussion of countermeasures. To address complaints and defects in the production process, we implement quality improvement activities, utilizing visual representation of information as a key method, and strive to make corrections and improvements with "Obeya" activities.
Production preparation activities / Quality Activity Study Group
During the entire process of new product introduction from product planning through to mass production, relevant parties conduct a design review at each step to confirm that the output is appropriate and to prevent defects from occurring during mass production. These activities are called "production preparation activities." We determine what needs to be done at each step, what needs to be confirmed, and who will be responsible for each activity, and establish a standard process through continuous improvement.
In FY2021, we launched the Quality Activity Study Group to make our production preparation activities more effective. The Study Group investigates defects associated with the production preparation process and promotes efforts for resolving fundamental problems by reviewing the conventional process and going back to production preparation activities, while holding discussions between the parties involved in the actual on-site production process.
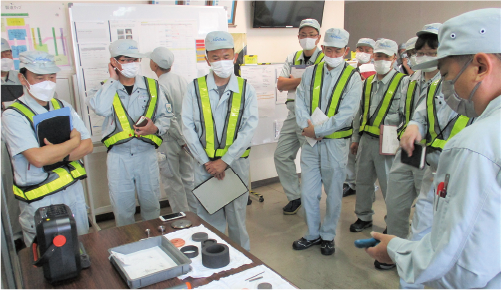
S3-1 Activities (Sales, technology, development, management, planning, and administration divisions)
The Noritake Group’s manufacturing enhancement activities are not limited to the plants at which we manufacture our products. In the pursuit of customer satisfaction, both the departments that directly face the customers such as Sales and Engineering and the administration and development departments that support these departments are involved in the making of products in one way or another. These manufacturing-enhancement activities carried out by our non-factory staff divisions are "S3-1" activities. S represents the S of service, and 3-1 represents the three "Firsts": Customer First, Quality First and Trust First, which our staff must always observe conscientiously as they carry out their work duties.
S3-1 activities are performed based on the awareness of these "Firsts", and are designed to elevate the quality of work.
The aim of S3-1 activities is to be able to "resolve problems and issues related to work autonomously and independently, with an awareness of customer satisfaction," and thereby increase the individual's problem-solving skills, and competitiveness of the company. All staff divisions are reviewing their operations from a customer perspective, aiming to improve operations in alignment with the ideal state. We place particular emphasis on reviewing operations through the "C" (check and review) aspect of the process. Through management reviews, feedback is provided from senior personnel to enhance the accuracy, quality, and efficiency of operations. This approach not only helps us maintain trust from our customers but enables us to create a more comfortable working environment. Engagement in these activities is also intended to improve employee awareness, leading to human resource development and building stronger organizational structures.
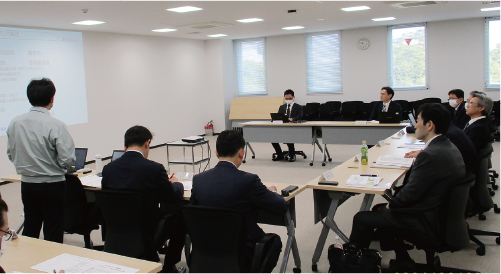
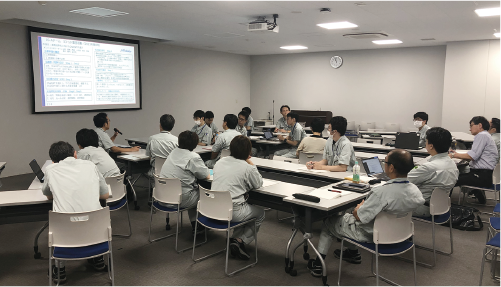
Communication with customers
In order to reflect customer feedback in our products and services, and to ensure that customers can use our products safely, we have set up a customer service center within the Tabletop Group to share customers’ opinions and inquiries with relevant departments in order to improve our products and services.
Product safety
The Noritake Group is committed to providing products and services that are safe and reliable from a customer’s standpoint. To ensure product safety, we observe relevant laws, regulations, standards, and/or voluntary standards throughout the product lifecycle, such as development, design, procurement, production, sales, and logistics. We shall also provide easily comprehensible labeling and user manuals to prevent potential accidents during the lifecycle, including disposing stage.